In lead smelters, rotary kilns are used to melt the input feed ( concentrate, lead sulfate, battery soil and all soils with acceptable lead grade). In most of these feeds, especially lead concentrate, according to the analyzes taken, we see a significant silver content (between 100 and 2500 ppm). After the feed is melted by rotary kilns, part of the incoming soil in the form of slag and tailings is removed from these kilns.
According to the analyzes taken from these wastes, it has been observed that there is about 80 to 110 ppm of silver in this tailings. Due to the high tonnage that is rotated daily in this factory, it can be concluded that a significant part of this silver will be lost in the tailings of smelting furnaces. The aim of this collection is to provide a suitable, engineered and possible solution to reduce the silver grade in the rotary kiln tailings.
The Challenge:
- Minimize the consumption of additives,
- minimize the melting time Prevent oxidation of silver,
- prevent the use of additives that could damage the refractory furnace,
- avoid methods that reduce the efficiency of lead extraction,
- maximum efficiency of silver mining along with economic efficiency
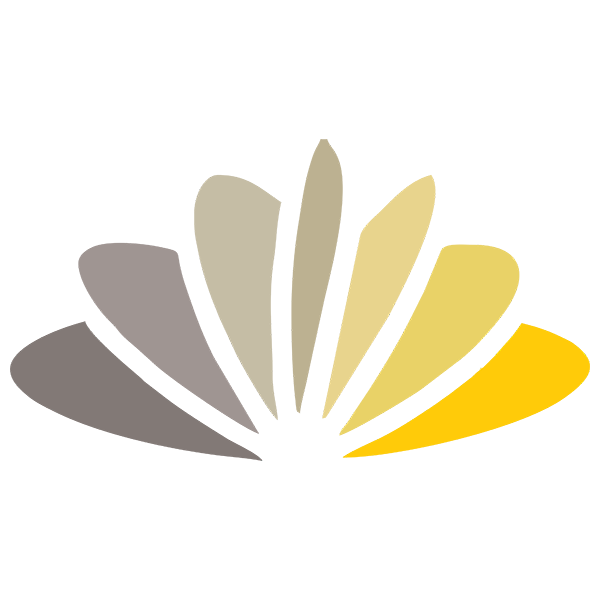
Zarrin Industrial & Mining Group
Islamic Republic of Iran